Blogs
Welcome to Beaver's Blog Page.
"Ripples In The Fabric Of Sand, Water & Time & Ripples in Ferro Rods! "
We recently had a very interesting enquiry from a Customer about his Ferro Rod and Combo Fire Striker. It’s a common problem with Ferro Rods that some people might not be aware off. So Mark decided to write a little blog about it..............
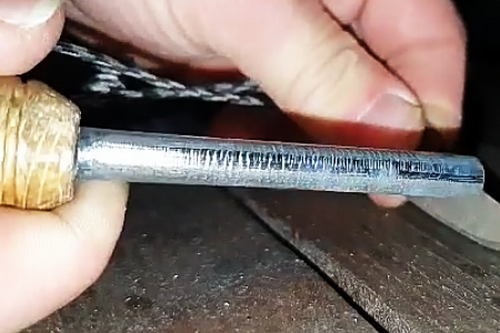
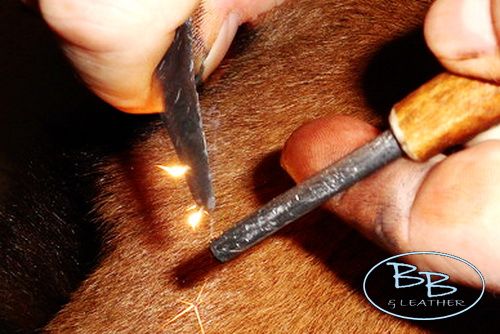
The Problem: Ferro Rods will ripple over time when scraped with a Striker. It is an unavoidable fact; it is just something that happens when any malleable surface is repeated scraped in such a way.
The ripples that are created on any malleable surface such as a Ferro Rod or Traditional Flint & Steel striker, for example, look like the ripples on a sandy beach when the tide is going out. If we use the sandy beach as an analogy for what is happening to our Ferro Rod when scraped with a striker over and over again. We will observe that these ripples are created, when the speed of water flowing over the sand grains causes some of the surface grains to become suspended in the water as it is flowing.
From this point on, any minor discrepancies, in speed of water flow will cause the water speed up and slow down into eddies. These eddies are sufficient to cause the heavier sand particles to fall out of suspension and begin to accumulate at that point, whilst on the other side of the eddy the water speeds up which allows more sand to be placed in suspension. This accumulation and dissipation of sand grains has a knock-on effect down the road that causes bigger eddies, which in turn causes more sand to accumulate ad dissipate at that point etcetera, etcetera, etcetera. Thus, over time, the fabric of the sand and water changes and ripples appear and then grow. So, it is with your Ferro Rod and your Striker! This phenomenon compounds itself over time and will only get worse unless rectified, and then it all begins again.
The Remedy : The only thing you can do is remove the ripples once they become noticeable, which is easily done in principle, by simply sanding or filing or grinding them away them away until you get a flat surface again.
The Caveat: However, since Ferro Rods are designed to create sparks when they are scraped even by sanding or filing or grinding them, you will need to be exceptionally mindful of any Ferro dust that will inevitably accumulating and then igniting when even the tiniest of Ferro dust particles accidentally but inexorably and spontaneously ignites, I would suggest that you place your Ferro rod in a vice and VERY, VERY carefully sand, file or grind it in one direction only and always away from your person, if you want to remove these ripples. It is important that you make sure that any filings created don’t land on something combustible and accumulate. You could try applying oil to the sandpaper or file so that you minimise oxidisation as the dust/filings are created, but this is quite messy and is still liable to cause a fire if the Ferrocerium particle ignite. Another way is to use a bench grinding wheel and let the sparks burn off into a bucket of water as they are created.
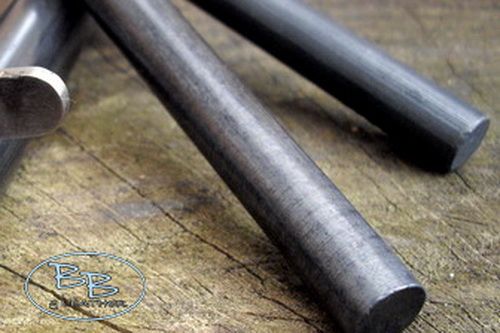
DISCLAIMER: Please understand that both methods, mentioned above will cause sparks that can easily burn your skin and set light to combustible materials within the range of any sparks created. SO, WE ADVISE EXTREME CAUTION and that if you attempt either of these methods, you do so at your own risk!
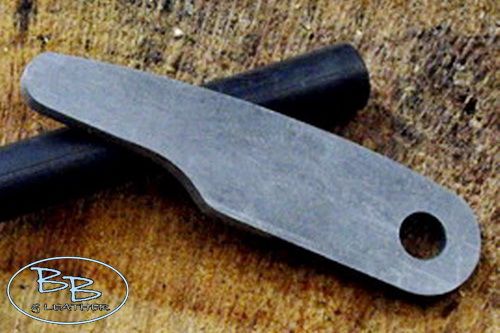
Introducing our Combo Fire Striker: The upper edge of our Combo Fire steel is designed for traditional Flint and Steel, hence the curved edge and the underneath section has been designed for using on Ferro rods. So make sure you use the correct edge or else these ripples on your Ferro Rod may get worse!
The Design of the Combo Fire Striker (the Science bit):
The long curved 90-degree edge part of the striker that you are using, in the videos, is used for Traditional Flint & Steel (TF&S) spark-based fire lighting, and not really intended to strike a Ferro rod efficiently.
Since the long-curved edge is intended for TF&S the 90-degree edges will have been very slightly rounded off a little to protect the Flint when striking the flint and steel together. All the others 90-degree edges, however, have been specially ground so that the edges are 90-degree sharp, which is to say, they are 90-degree sharp so they can easily and efficiently scrape Ferro rods, but cannot accidentally cut people.
Please see our web page listing, for more info and videos on using our Combination Ferro Rod Strikers and may your ripples disappear like the sands of time!
"Happy Fire Lighting "
"How we make our hand crafted Leather Bottles"
How we make our beautifully hand crafted leather bottles at Beaver Bushcraft........
Whether they are for Film sets, TV programs, Museums, Collectors or for personal use, our traditional style handmade leather bottles are certainly becoming more and more popular. Made using only the very best vegetable tanned leather, bees wax and pine resin our traditional leather bottles are all made by hand in our Kent based Workshop. Each bottle is individually cut, stitched, wet-formed & then waxed by us, in-house, from start to finish. This allows us to have full control over the manufacturing process, which effectively means that we can guarantee that each bottle that we make is superior quality.
It takes us approximately 7 to 10 days to make each leather bottle. We carefully select matching, left and right handed leather bottle blanks from a single hide of leather that will allow us to homogenously wet form a leather bottle, after they have been carefully sewn together.
During the wet-forming process each bottle is individually assessed and then carefully shaped, to enhance its own natural characteristics. It is carefully formed into a beautiful and unique, yet consistently accurate traditional leather bottle shape. Picture on the left right shows Mark shaping one of our bottles by hand.
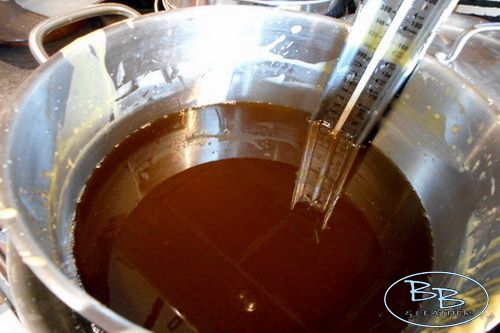
Once the bottles have naturally dried for at least week, they are then fully submerged and impregnated in a full immersion in a bees wax or Brwers Pitch bath, before being fully lined and sealed with more wax. Picture on the right shows getting the wax to the correct temperature, this is most crucial that the heat is just right! The wax we use is totally food safe.
Once the bottles are fully harden, we can then attend to the final stages of the manufacturing process before they are finished off by giving them a good polishing and then buffing with a soft cloth. As you can see they certainly are a labour of love!
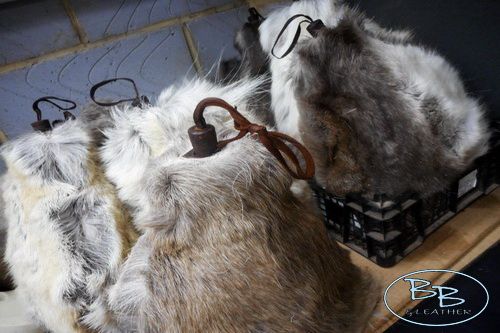
Reindeer Skin Covered Bottles we made for the film "The Huntsman"
Personalised Leather Bottles we made for Pippa Middleton
We made a load of mini leather bottles as Gifts for a woodland wedding
A batch of Leather Bottles hanging up to dry for the TV Show "10'000 BC"
A Brief History of Leather Bottles:
We at Beaver Bushcraft like the idea of continuing traditional skills, particularly the tradition of making leather bottles. Leather bottles – as opposed to animal bladders and intestines - have been in use since the Neolithic period and probably earlier if the truth be known, when they discovered that leather/skins could be shaped by wetting the leather and letting it hardened by boiling it or leaving out in the heat of the sun.
It could be said, that leather very much was the material of choice, for the personal transportation of small quantities of liquids, from the earliest days of Human history right up to Tudor times and beyond, for its availability, durability and lightness of weight. Certainly, by way of contrast, leather bottles, would have been much easier to make and to carry than the heavier more fragile, and without being fully glazed, porous in nature earthenware pots of the time. Throughout history, leather bottles have been adapted, shaped and designed to suit their purpose. For example the leather bottles found on the wreckage of Tudor ship the Mary Rose, where made wider and flatter on the bottom to stop them rolling around whilst at sea. The photo above right shows a copy we made of one of the Bottles found on the Mary Rose. We deliberately made it look very old and rustic.
During Elizabethan times, it was only the rich that could have afforded genuine glass wine glasses due to the high cost of glass and the skills needed to make them. Wine glasses would constantly have been filled by a servant holding a leather bottle who was known at the time as the ‘Botellar’, a term and position in life today that is more familiarly known as a ‘Butler’. In the village of Hallaton, Northamptonshire, the sport of bottle kicking was very popular. The bottle was originally made of leather making one wonders, if this was the origin of the leather football !!!
Early Eastern ‘primitive’ leather bottles were really just a ‘bag’ made from tanned or untanned skins of entire animals, such as kid, goat, cow, camel or buffalo. And i n most cases made from the animal entire body, after the legs and head were cut off and sewn or tied closed!!! When filled, these leather bag bottles grotesquely retained the shape of the animal. The Photo above shows a modern version of a bottle made from the skin of an animal. Certainly the use of whole hide bottle bags is still widely used by nomadic Mongolian tribes, who often use them for storing fermented milk, butter and cheese’s as well as water.
Other bottle bags used by our ancestors for storing wine or oil would have been tanned by plants rich in tannins such Oak bark and leaves etc & then seasoned in smoke, a process that apparently gave a rather peculiar tang to the flavour to the wine. I’m glad to say the process of storing these liquids has become more sophisticated since then, especially since the invention and widespread availability of glass!
How Leather Bottles Have Shaped Our History......
We have already mentioned the word ‘Botellar’ and how it changed into the word ‘Butler’. The Bottle on left shows one of our hand stitched traditional style leather Flask.
When Leather is worked wet (so that it can be shaped) and then air dried, it becomes what is known as ‘Jack Leather’ and medieval leather drinking utensils thus became known as ‘Jacks’. The use of the word ‘Jack’ continued until Nelson’s time when they were known as ‘Jack Boots’, hence the naval phrase "Fill up your Boots" meaning "have a drink"!!!!. In fact the term ‘Jack boots’ is still used to this day ‘German Jack Boots’ is a good example.
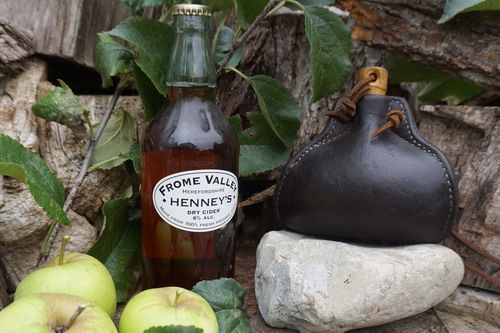
We love the way leather bottles as well as leather drinking vessels have helped shaped the social drinking habits through the ages and we at Beaver Bushcraft just love the idea of continuing this great tradition and keeping this ancient skill alive. Many people still make leather bottles to do this day and we like to think our hand crafted leather bottles will the heirlooms of the future & bringing back a little bit of history to life.
Hudson Bay Tinderboxes & Boris Blog !!!
Not sure how many people are aware of the situation with the new trade deals between the UK, USA and the EU. Sadly it’s impacting everyone, especially small business due to the difficulties of importing & exporting, not to mention the UK want the USA to register for VAT in this country! This is affecting some of the raw materials we need but most of all, our beloved Hudson Bay Tinderboxes. We are looking at a way to import them in from the USA without involving heavy masses of paperwork not to mention the high costs of Import Duty, VAT etc. So meanwhile we have had to come up with an alternative ourselves. Saying that, we have also wanted to make these for a very long time now…..our very own ‘Beaver Creek’ Tinderboxes!!! Beautifully hand crafted from vintage leather. We have built in a high spec solar lens into the lid and have added a leather lens cap to protect the glass.
Inside you will find a traditional Flint & Steel fire lighting kit! Everything to capture and make fire like the old pioneers used to! Just like the Hudson Bay tinderboxes, our leather hand crafted Tinderboxes are designed to be used and the more you use them the better they will look over time!
We will still be selling the Hudson Bays, in fact we have recently managed to get hold of a few pre-loved ones. These will be available in our Vintage & Preloved section of the website in a few weeks!
Meanwhile we are working on a solution to try and get the Hudson Bays into the UK without incurring a huge amount of fees!!!! Watch this space.